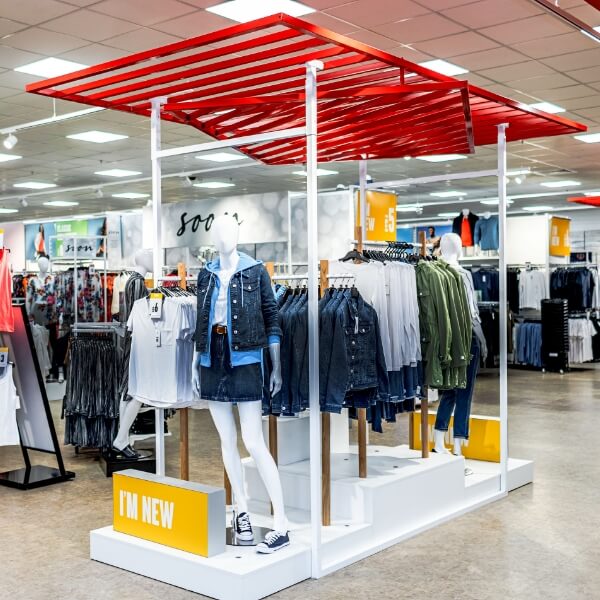
ETHICAL SUPPLY CHAIN:
Ensuring High Standards
Looking after the people who produce our goods is our absolute priority. We will only do business with suppliers who we believe share our values, respect people and champion human rights.
Although we don’t own the farms, processing facilities or factories that produce the garments and goods that we sell in our stores, we have a robust screening process in place to make sure our contracted suppliers are acting ethically. It’s important that all of our supply base demonstrate that they uphold the rights of their workers and offer fair pay in safe working conditions.
Monitoring ethical standards is complex task that requires constant vigilance. Our experienced ethical compliance team continually monitors the factories where our products are made, and are able to carry out ad-hoc spot checks when necessary. This team is supported by external experts based in the UK and in the countries we source our products from. We use data platforms shared with other retailers to collate an accurate picture of supplier performance. Importantly, we build long-standing relationships with our suppliers and collaborate with them on health, safety and ethical performance.
Ethical compliance is everyone’s responsibility at Matalan. We provide training for colleagues on how to spot and report concerns around modern slavery. This training is mandatory for our buying and sourcing teams. We train our buying teams to look for good practice when they’re meeting with suppliers, and how to report any concerns.
Our Actions
Doing business ethically runs through all of our day-to-day interactions with suppliers. There are four key stages in our relationships to help measure and mange compliance with our standards.
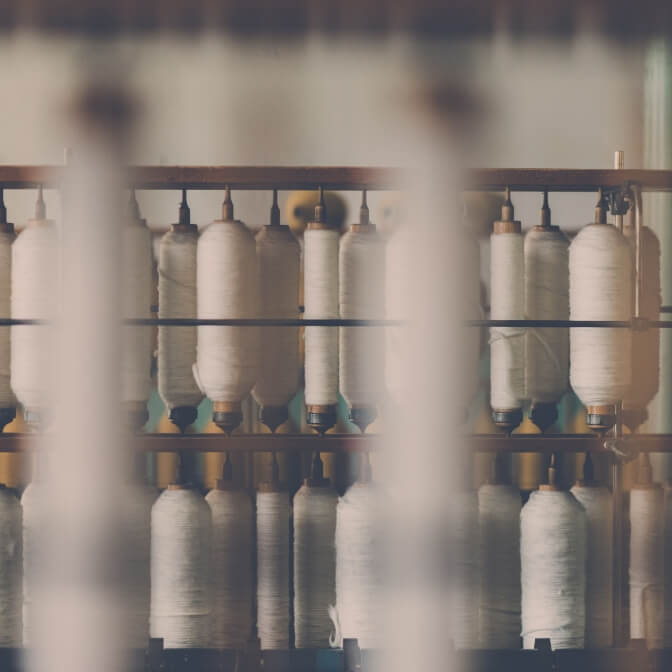
Due diligence at the start of a relationship
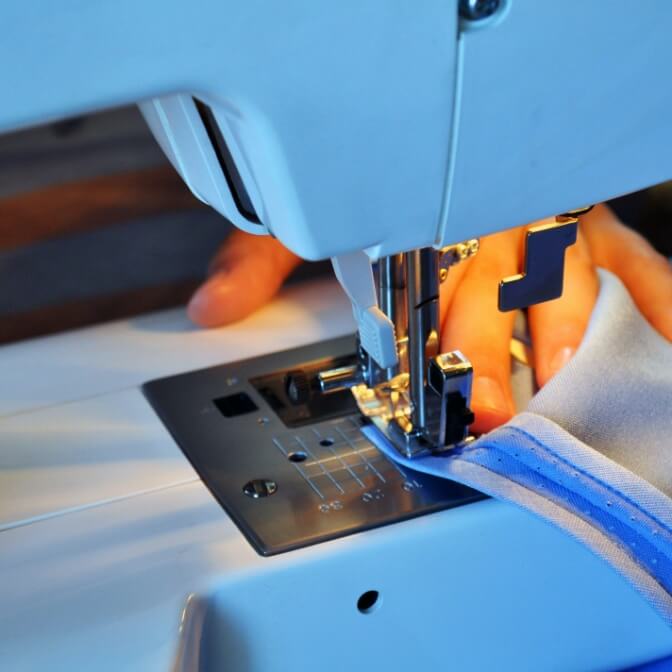
Regular monitoring throughout our contract
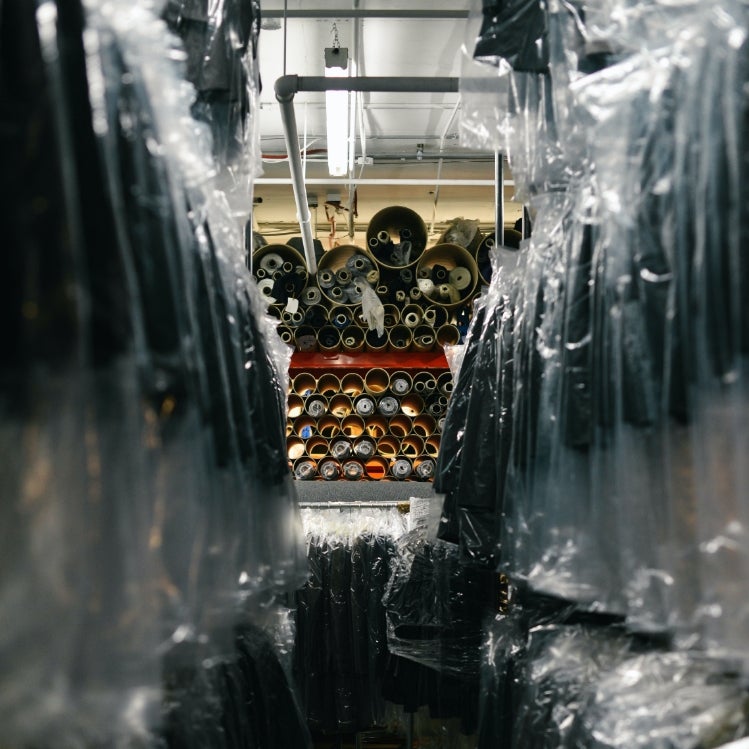
Times when improvement is needed
Should any issues be identified during these audits, the auditors will recommend a Corrective Action Plan (CAP) and we agree a completion timescale with the factory. This is uploaded to the Sedex platform as a record and for monitoring progress. As part of our due diligence program, the factory is required to upload evidence that any non-compliance issues have been closed and verified by the audit company for assessment by our Ethical team. At this point our Ethical trading team will review the case and decide if further actions needed, for example, more frequent or enhanced auditing, visits by the team to the factory.
- We have three levels of corrective action plans – minor, major and critical
- In 2021-2022 of over 800 audits completed, 12 identified critical issues with our suppliers
- Depending on the nature of the corrective action needed, our suppliers have either 30, 60 or 180 days to demonstrate that they have resolved issues and are complaint with our standards
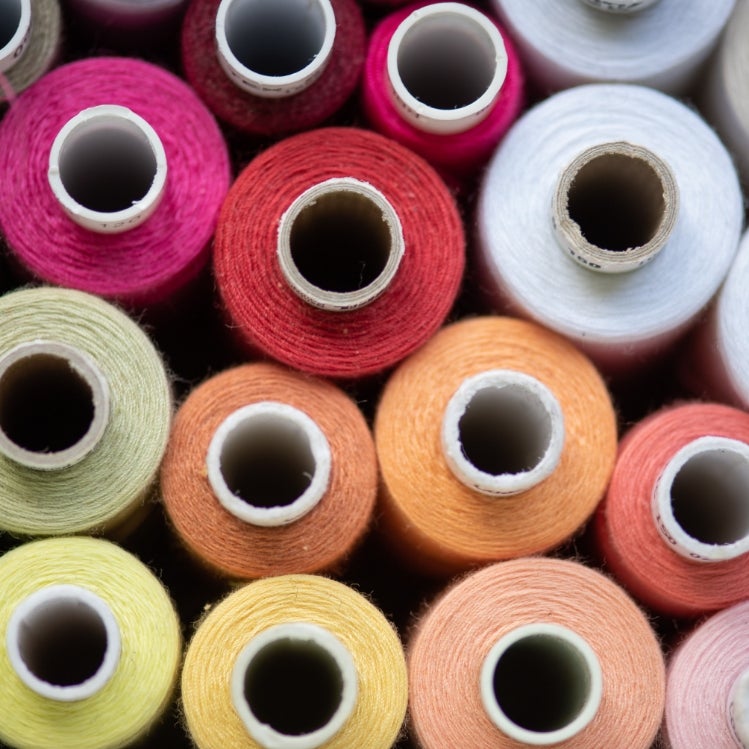
When our standards are not met or maintained
We believe our suppliers, and the communities that rely on them for their employment, benefit from stable work and business certainty, and we want to work with factories and suppliers to fix issues that come up. However, the safety and wellbeing of workers is paramount and we will always take decisive action to stop working with factories that are not able to demonstrate that they consistently meet our standards, or any factories where a serious breach is identified.
In these rare circumstances, we have a responsible exit policy that we follow. This helps minimise the disruption or interruption to workers as much as possible. When we exit a relationship, we use our influence with the supplier to make sure the leadership team:
- Engages with worker representative groups
- Consults before making decisions about employment
- Objectively and fairly selects workers for termination if that is unavoidable
- Pays severance compensation according to local law and shows documentation of the settlement